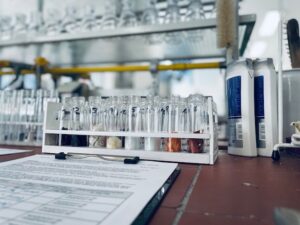
Nickel release
DIN EN 1811 describes a method for determining the release of nickel of metal parts. For coated metals, an abrasion process according to DIN EN ISO 12472 is carried out beforehand. This test is provided for all metal products that are either pierced (such as earrings) through the skin, or have otherwise prolonged skin contact, such as button for trousers and jeans.